Maximize Construction Excellence with E14 Engineered Wood LVL Beams (200 x 45mm)
In the fast-paced world of building materials, innovation is a continual driving force. Engineered wood products have transformed the industry by improving structural performance, adaptability, and sustainability. Among them, the H2S-treated SENSO Framing LVL F17 beams, notably the E14 Manufactured Wood LVL Beam with dimensions of 200 x 45mm, have emerged as a must-have for architects, builders, and engineers. These beams combine rigorous engineering and preservation technology to provide a strong solution for a variety of building applications.
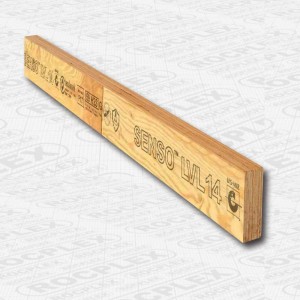


Components of H2S Treated SENSO Framing LVL F17 Beams:
- Engineered Wood LVL: The heart of these beams lies in their engineered wood composition. Laminated Veneer Lumber (LVL) is crafted by bonding layers of wood veneers using advanced adhesives. This manufacturing process enhances the material’s strength, stability, and resistance to common issues like warping and splitting, ensuring reliable and predictable performance.
- H2S Treatment: The H2S treatment is a critical component that significantly enhances the beams’ longevity and durability. This treatment involves impregnating the wood with preservatives that ward off threats like decay, termites, and fungal growth. This protective barrier ensures the beams’ structural integrity even in demanding environments, making them suitable for various applications.
- SENSO Framing: SENSO Framing is a hallmark of quality and expertise in engineered wood products. Their LVL F17 beams meet stringent structural grade requirements, assuring architects and builders of dependable load-bearing capacity and performance. SENSO’s commitment to sustainability and precision engineering further elevates the beams’ overall value.
Benefits of E14 Engineered Wood LVL Beams (200 x 45mm) with H2S Treatment:
- Exceptional Strength: Supports heavy loads for safe and robust designs in various applications.
- Longevity: H2S treatment enhances durability, resisting moisture, pests, and decay for extended service life.
- Dimensional Stability: Engineered wood minimizes warping, ensuring accurate construction over time.
- Design Flexibility: Impressive load-bearing capacity allows longer spans, facilitating open and pleasing spaces.
- Sustainability: Engineered wood and H2S treatment promote eco-conscious practices by optimizing timber use and protection against decay and pests
Refer to the Specifications below for specifications on the major types of LVL formwork supplied by ROCPLEX or contact us to discuss further your needs.



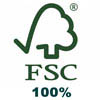
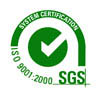


Please contact our sales team for more detailed information regarding ROCPLEX – SENSO Structural LVL.
LVL Beams 200 x 45mm FAQ
Q: What is the maximum span for a 200 x 45mm LVL beam?
A: The maximum span for an LVL beam depends on several factors such as the load it will bear, the type of support at each end, and the spacing between supports. Typically, a 200 x 45mm LVL beam can span up to 3-4 meters with appropriate support.
Q: How are LVL beams installed?
A: LVL beams are typically installed by attaching them to supporting structures, such as walls or columns, using appropriate connectors or fasteners. They can be bolted, screwed, or nailed to the supporting structures, depending on the specific application and load requirements.
Q: Are LVL beams resistant to moisture and insects?
A: LVL beams are typically treated with preservatives to protect against moisture and insects. However, it’s still important to follow appropriate installation guidelines to minimize exposure to moisture and maintain the integrity of the beam.
Q: Can LVL beams be cut to size on-site?
A: Yes, LVL beams can be cut to size on-site using standard woodworking tools such as saws. However, it’s important to follow the manufacturer’s instructions for cutting and drilling to avoid damaging the beam’s integrity.
Q: Are LVL beams environmentally friendly?
A: LVL beams are considered to be a sustainable and environmentally friendly building material since they are made from renewable wood resources and can be recycled at the end of their lifespan. Additionally, the manufacturing process for LVL beams produces less waste compared to traditional solid timber beams.